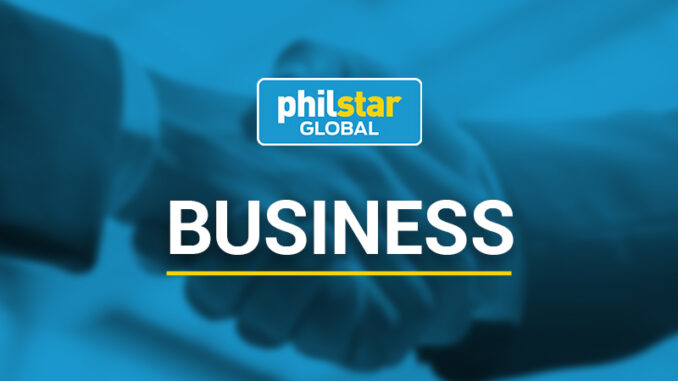
Lorraine (not her real name) is a friend on Facebook. She’s a human resource (HR) manager of a small factory who inquired about my free management consultation.
I agreed on the condition that we do the consultation via Zoom as it offers the best service to all busy managers – it limits conversations to 40 minutes.
She asked: “How do we make our workers productive for the last 15 minutes before clocking out?” I took a peek at her profile picture showing her Mona Lisa smile which is often interpreted as a half-smile and half-grief at the same time by many people.
Suddenly, I remembered my experience with male and female workers. The male workers would start preparing to leave the office premises 15 minutes early under the guise of an extended toilet break.
Their female counterparts do it 25 minutes early. The routine is often repeated in the morning when both genders punch their fingers in the biometric system.
Lorraine was tasked to resolve the problem of the workers doing unproductive things before they clock out at 4 p.m., Monday through Friday. When factory operators are on the last batch of drying a product, it gives them an average of 15 minutes waiting time before the 4 p.m. bell.
When the workers were seated doing nothing, they were charged for violating their code of conduct against doing unproductive work. Their usual defense was “drying time” of a product they’re making for the day.
I told Lorraine that penalizing the workers for their idle time would not solve the issue. “How about cleaning their work station?” I asked Lorraine. She replied there’s not much to clean. If there was, the cleaning can be done in three minutes or less. That leaves us with 12 unproductive minutes.
Thinking people strategy
I’m not privy to their factory operations so I can’t give them specific solutions so I gave Lorraine some generic advice. I told her to require each and every worker to use the remaining 12 to 15 minutes to reflect on what they’ve accomplished or mis-accomplished for the day. If they’ve 100 workers, that means a total of 100 daily reflections on what they perceive to be issues and opportunities that management should handle right away. I call it as the Thinking People Strategy (TPS) where organizations must create, nurture and maintain an army of employee problem-solvers.
In doing TPS, I proposed that they require their workers to use their idle time to work on any idea, opportunity or even a complaint about anything. To make it easy for the workers, they must accomplish a simple and easy-to-fill-up form according to the following basic parameters – safety, health, environment, quality, cost, delivery and productivity.
All ideas must be reviewed by the workers’ direct boss who is given one day to vet their ideas. If accepted, line management has the option to pass it on to an ad hoc committee for further evaluation. If there’s no required budget for its implementation and all stakeholders agree to it, an idea is implemented without delay.
If a boss is absent or fails to act on any idea for any reason, it is automatically elevated to the next ranking official whose decision is final and non-appealable.
What are you thinking about this advice? If we’re talking of a conservative number of 100 workers giving 100 ideas every day, that means 2,000 ideas per month. Is your organization capable of handling this program that would amount to producing 24,000 ideas in one year?
TPS program
That’s the biggest challenge. However, that’s nothing compared to all the advantages and benefits you can get out of the program. Even if you get only 5,000 excellent ideas out of the 24,000 submitted, that could translate to a healthy and safe workplace, improved product quality and labor productivity, surely, a definite advantage for any organization.
It must be worth the effort provided the following interventions are done prior to the implementation of a TPS program:
One, seek top management approval. If approved by the chief executive officer and members of the senior management team, then how could you go wrong with it? If you have the backing of the senior executive team, it would be smooth sailing for you.Two, volunteer as the TPS administrator. The program needs a secretariat to handle the program smoothly and systematically. This requires a simple and inexpensive software to record and monitor all employee ideas that are submitted.
Three, conduct an orientation program. Two separate schedules may be done for the team leaders, line supervisors and managers in one batch and a different schedule for the factory workers who may have a different agenda and interest with their bosses.
Four, allow a pilot execution for the first month. This is beneficial not only for the line leaders and their workers but also to the TPS administrator who can monitor and adjust the system and its form, if necessary.
Five, give appropriate reward and recognition. Management may give cash or non-material reward to those who deserve it. Without a semblance of recognition, it would be difficult for management to secure greater employee engagement.
Lorraine thanked me profusely and concluded with a poop emoji in our chat. When I asked her about it, she deeply apologized for her mistake. She thought it was an unwrapped Hershey’s Kisses chocolate.
Rey Elbo is a quality and productivity improvement enthusiast. For free consultations, email your concerns to [email protected] or via https://reyelbo.com. Anonymity is guaranteed.
Be the first to comment