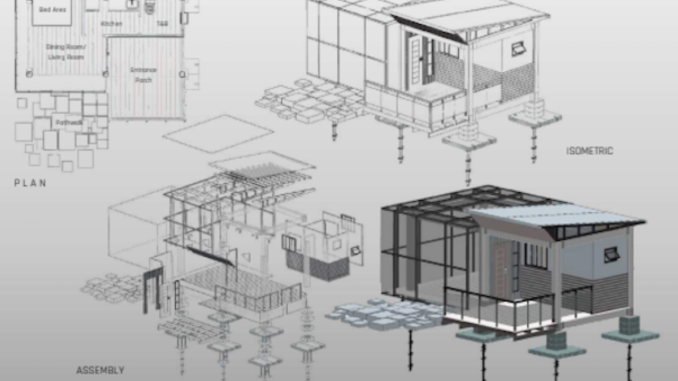
SINGAPORE-BASED property technology firm Homeqube is gearing up to deliver and address the increasing housing backlog of the country by offering Filipinos faster homebuilding and affordable, but sturdy, homes using blockchain and artificial intelligence (AI).
Starting Nov. 18, its self-service showroom in Makati will be open to the public to experience homebuilding through the integration of AI and blockchain.
BUILD YOUR OWN. Home buyers can order their home in Homeqube on their website for as low as P1 million up to P15 million varying on 45 customizable designs. GRAPHIC PHOTO FROM HOMEQUBE
“Throughout the showroom, you will find QR codes that provide seamless access to essential resources, including installation request forms and information on financing options,” Homeqube said on its Facebook page $QUBE.
The immersive experience was designed to help clients visualize their dream home while understanding sustainable and cost-effective solutions that could make home ownership a reality.
Jose Paolo Calma, Homeqube founder and chief executive, told reporters in October that Homeqube will “industrialize the home industry through parts” using glass fiber reinforced polymer (GFRP), a lightweight material that could be easily transported to any location of the home buyer’s choice.
“By choosing materials that regenerate, we can create a more resilient and adaptable environment, ensuring that our build environment remains a testament to our evolving needs,” Calma said.
With the $1 million investment of Calma, the company aims to lessen the abundant use of steel and cement for building a house, which for him was too bulky and complex to transport that leads to a higher cost for people to build their home.
“Whereas, if your materials are lightweight, like Lego, you can take it with you,” he noted, adding that “you can erect a house anywhere, far from [the center], off-grid [locations].”
Homeqube boasts its home delivery service online, where home buyers can buy a home to be delivered on any type of land they have acquired, such as beachfronts, farm fields, or even residential subdivisions, in just under six months, from permitting phase, to the acquisition of materials, to the 30-day installation and delivery.
Home buyers can order their home in Homeqube on their website for as low as P1 million up to P15 million, varying on 45 designs that are customizable on client’s design structures.
This service helped buyers secure their homes in a faster turnover time than the longer 18-month lead time on traditional home building, resulting in a more expensive project cost due to logistics and middleman fees.
The homes that will be built by Homeqube are said to be producing less carbon emissions and cutting the environmental footprint of building projects, which is the best choice for assemble-to-order manufacturing strategies.
Calma further noted that despite GFRP’s components being lightweight, the material can withstand harsh weather conditions experienced in the Philippines up to 310 kilometers per hour of strong winds.
The materials being used are also rust-proof that makes material transportation easier via boat.
Transporting materials between islands in the country made homebuilding more expensive. For Homeqube, its investment in a carbon kevlar cargo boat ensures delivery of homes anywhere in the 7,561 islands of the country.
“We have a boat, the first carbon kevlar cargo boat in the Philippines,” he said, which is also set for sea trial this month.
Calma hopes for Homeqube to deliver 1,000 housing units for their first year, as their current production plant can only take up to 3,000 orders per year.
Calma noted that after the successful launch of Homeqube and its establishment in the market, Homeqube will introduce a Web3-based “paluwagan” concept for players using its own blockchain token as a mode of payment; they will be ranked based on the amount of contribution and will be awarded a Homeqube house, leased for up to 35 years.
Be the first to comment